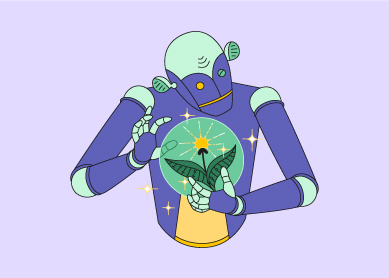
How ML Can be Used in Predictive Maintenance for Green Tech Solutions?
Contents
Contents
Machine learning has emerged as a true game-changer in Industry 4.0. The technology allowed companies to shift from traditional reactive approaches to proactive strategies that anticipate and address issues before they escalate. Driven by the need for increased efficiency, reduced downtime, and resource optimization, predictive maintenance is now not just an advantage but a necessity.
Moreover, ML-driven predictive maintenance became a natural step in businesses exploring sustainable technology since the traditional “break-fix” model wasn’t sufficient for those leaning toward greener and more environmentally friendly solutions.
As ML algorithms become more advanced, businesses get more opportunities to harness data for smarter decision-making. By predicting equipment failures before they occur, we can schedule targeted maintenance, reduce the need for emergency repairs, lower energy consumption, and contribute to a more sustainable operational framework.
In this article, we explore how exactly machine learning for predictive maintenance works in practice and how you can leverage these solutions within your organization.
Understanding ML in Predictive Maintenance
Firstly, we need to determine the value of machine learning in predictive maintenance. The use of ML involves analyzing vast amounts of data from sensors, IoT devices, historical records, and other sources to identify patterns that indicate potential equipment failures. ML algorithms learn from this data to then recognize abnormalities and predict when maintenance is likely to be required.
For instance, in solar power facilities that use ML, panel sensors collect data on various parameters. ML algorithms analyze this information to predict potential issues, such as deteriorating panel efficiency or faulty components. By proactively scheduling maintenance based on these predictions, the facility can ensure optimal energy production and enhance the overall efficiency of renewable energy generation. This practical ML application transforms maintenance from a reactive to a proactive and data-driven strategy.
Now, let’s see how much impact this technology can make based on the approach’s popularity.
- Due to the increasing adoption of AI and ML, the global predictive maintenance market is projected to reach $31,965.49 million by 2027, growing at a CAGR of 28.8% from 2020 to 2027.
- According to McKinsey’s survey of 100 senior leaders responsible for equipment maintenance and asset productivity at their organizations, 84 percent of respondents already adopt predictive maintenance approaches for critical assets. In companies with mature reliability-centered maintenance (RCM) capabilities, around 70 to 85 percent of technician hours are spent on preventative maintenance (PM) activities.
- The Clarified startup, which provides AI-driven predictive maintenance solutions, claims impressive numbers on the technology’s impact: potential 25% cost reduction, 35% less downtime, and a 10x return on the initial tech investment.
Traditional vs ML-Driven Maintenance
Traditionally, maintenance was reactive – something breaks, and then it’s fixed. It also could involve predefined maintenance schedules; however, those led to over-maintenance or missed opportunities for timely intervention. Such an approach often came with unplanned downtime, increased costs, and a less-than-ideal environmental footprint.
The use of machine learning introduced a much more dynamic and adaptive model. By continuously analyzing data, ML algorithms predict when equipment will likely fail, allowing for precisely timed maintenance. Here is a comparison of traditional and ML-powered approaches to maintenance.
Traditional maintenance | ML-driven predictive maintenance |
Reactive approach | Proactive intervention |
Fixed maintenance schedule | Dynamic and adaptive maintenance |
Routine checks | Real-time health monitoring |
Limited data handling | Analysis of large datasets |
Unplanned downtime | Predictions of failures in advance |
Increased costs | Optimized operational efficiency |
Based on this table, ML-driven maintenance not only enhances the longevity and efficiency of critical assets but also significantly minimizes environmental impact, making it essential for green tech innovators.

Use Cases: ML Transforming Industries
The most obvious industry that benefits from predictive maintenance is manufacturing. However, the list includes other sectors, including healthcare, transportation, telecommunications, mining, and facility management. Below, we focus on the most widespread use cases and ML predictive maintenance case studies to support them.
Healthcare
One of the primary tasks of ML for healthcare equipment maintenance is advancing the reliability of life-critical devices. In hospitals, predictive maintenance algorithms are used to analyze data from medical equipment, ensuring that vital machines such as MRI scanners and assisted ventilation systems remain operational. By anticipating potential failures, healthcare providers can proactively address issues, ensuring patients always get the care they need.
Siemens Healthineers, a global leader in medical technology, has embraced ML to enhance the reliability of critical medical devices. In collaboration with hospitals, their predictive maintenance solutions analyze data from sensors embedded in medical equipment. The company also partnered with SAS, resulting in the development of the MindSphere platform. This collaboration integrates advanced analytics from SAS into MindSphere, accelerating the use of machine learning and AI. With improved data processing capabilities, Siemens Healthineers aims to offer better field service, creating more advanced predictive models for heightened efficiency.
Another case is Kashiwa Health Check Clinic, which, in collaboration with Hitachi, implemented a predictive maintenance system for its MRI machines, reducing downtime by 16.3%. Hitachi analyzed three years of sensor data from 100 MRI systems, using ML to define normal operational states, anticipate abnormalities, and detect changes leading to failures.
Aviation
In the aviation industry, where safety is critical, ML-powered predictive analytics is typically used for real-time monitoring of aircraft components. By analyzing data from sensors and historical performance, ML algorithms predict when specific parts may require attention. This approach helps ensure the safety of flights while also optimizing maintenance schedules, reducing costs and environmental impact.
By 2025, more than 38,000 aircraft are forecasted to be in operation worldwide. Maintaining all of them the traditional way is becoming simply impossible. Therefore, reliable airlines now partner with ML developers to ensure flight safety. For instance, Lufthansa was able to decrease device failures and reduce total downtime by over 20% with predictive maintenance solutions.
Energy
In the energy sector, including green tech, ML-powered predictive maintenance analyzes data from sensors and devices deployed in critical infrastructure such as wind turbines, solar panels, and power grids. These systems continuously collect and transmit vast amounts of data, not just on equipment performance but also on environmental conditions.
As a strategic move, Vestas, one of the world’s largest wind turbine manufacturers, acquired Utopus Insights Inc., an energy analytics provider. This acquisition allowed the company to provide customers with a suite of top-notch analytics products, facilitating the digitalization of renewable energy assets and systems. A part of this suite is predictive maintenance tools that leverage ML to optimize the performance of wind turbines in their wind farms.
Manufacturing
Naturally, we couldn’t make this list and not mention manufacturing. The integration of ML in predictive maintenance has become a game-changer for factories and plants. By monitoring machinery and production lines in real time, manufacturers predict equipment failures before they occur, minimizing downtime and optimizing maintenance activities.
Some companies go even further. Bosch, a multinational engineering and technology company, uses ML in more innovative ways, such as edge computing and digital twins. In smart manufacturing facilities, Bosch leverages edge computing for real-time analysis of machine data, enabling immediate responses to potential issues. Additionally, Bosch employs digital twins to create virtual replicas of critical infrastructure, facilitating simulations and predictive modeling for more informed maintenance strategies.
Transportation
The primary job of ML-powered predictive maintenance in the transportation sector is enhancing the reliability of vehicles and infrastructure. It typically involves real-time vehicle health monitoring through sensor data, predicting component failures to optimize maintenance schedules, and improving fleet reliability. For instance, fleet operators use predictive maintenance to keep vehicles on the road with minimal disruptions.
Companies like UPS use ML algorithms to analyze real-time sensor data on its extensive fleet of delivery vehicles. By predicting and preventing potential breakdowns, they can schedule timely repairs, minimize disruptions, and ensure the reliability of transportation services.
Automotive companies are also worth mentioning in this case. They use ML to anticipate maintenance opportunities and retain customers, encouraging them to seek maintenance services from the car manufacturer’s official network. For example, Opel’s vehicles are equipped with predictive maintenance tools that analyze historical data to suggest optimal inspection schedules, notify drivers when maintenance is due, and arrange appointments with the official network.
This list above is far from comprehensive: ML for predictive maintenance can also benefit agriculture, construction, hospitality, defense and military, and more. But no matter where it is used, this approach is a pathway to optimizing business operations and contributing to a more sustainable future of industrial maintenance.

Machine Learning for Sustainable Business Practices
ML-enabled predictive maintenance is typically associated with a sustainable approach to business operations. But how exactly are they connected? The table below lists the best practices in ML-driven maintenance and explains how they enable a more eco-conscious way of conducting business.
Sustainable business practices with ML for predictive maintenance | |
Proactive fault detection | Analyzing data from sensors and historical records to detect and address potential equipment failures before they occur, thus optimizing resource utilization |
Extended asset lifespan | Identifying optimal operating conditions for machinery to extend the lifespan of critical assets, promoting responsible consumption and thus aligning with the circular economy model |
Sustainable waste management | Preventing unexpected breakdowns to minimize the disposal of irreparable equipment components and reduce electronic waste |
Energy efficiency | Analyzing data to identify optimal operating parameters, fine-tune operations, and reduce energy consumption, which contributes to a lower carbon footprint |
Strategic resource allocation | Allocating resources in a way that prevents unnecessary downtime and emergency repairs, optimizes resource consumption, and contributes to sustainable operational practices |
By adopting these sustainable predictive maintenance practices, businesses can actively contribute to sustainability goals.
ML-based predictive maintenance is also vital in the context of green tech. For instance, by embracing this approach, companies can extend the lifespan of components like aircraft engines and lithium-ion batteries. Moreover, the application of predictive maintenance in optimizing energy consumption showcases the potential for substantial energy savings and contributes to overarching sustainability goals.
We already mentioned how companies in various industries leverage ML-enabled predictive maintenance. However, the developers of such systems are also worth highlighting in this article. Based in Singapore, WaveScan specializes in developing innovative beamforming electromagnetics-based smart sensor systems and advanced AI algorithms. They’ve developed wireless sensors using advanced technology for non-destructive testing, providing a complete AI-enabled solution for asset inspection in the built environment. WaveScan aims to create safer and more efficient cities by revolutionizing how infrastructure is maintained through establishing a predictive maintenance ecosystem.
Challenges and Solutions to Implementing ML in Predictive Maintenance
As it happens with the introduction of any new technology, there are certain challenges in ML implementation for predictive maintenance. Along with acknowledging them, we offer you best practices to help you navigate the complexities of ML adoption.
Data Quality and Availability
The accuracy and reliability of machine learning models heavily depend on the quality of input data. However, ensuring the availability of high-quality data for ML-powered predictive maintenance can be challenging due to factors like data fragmentation and inconsistencies. Obtaining a consistent and reliable dataset from various sources may require substantial preprocessing and quality control effort.
As a solution, we recommend prioritizing data governance to ensure data quality and availability. It’s also essential to implement rigorous preprocessing techniques to handle outliers, missing values, and inconsistencies, enhancing the reliability of predictive models.

Integration with Existing Systems
Integrating ML solutions seamlessly into existing maintenance processes and systems can be a logistical challenge due to legacy systems’ diverse and sometimes rigid architectures. Let’s say an organization relies on outdated CMMS (Computerized Maintenance Management System) software that lacks advanced analytics capabilities. Integrating a state-of-the-art ML predictive maintenance solution would be challenging, requiring updates or replacements to the existing software infrastructure to align with modern data-driven methodologies.
In such cases, it makes sense to embrace gradual integration. You can approach ML implementation incrementally, starting with pilot projects and gradually expanding to larger-scale integration. This allows for thorough testing, identification of potential challenges, and system refinement before full deployment.
Scalability
Diverse assets and systems within an organization, especially a large enterprise, often have unique characteristics, requiring tailored models for effective predictions. Therefore, implementing ML for predictive maintenance across an entire organization requires scalable solutions, which can be challenging.
To address this issue, you can tailor ML models and algorithms to the specific predictive maintenance requirements for different assets. Customization ensures that the models can effectively address diverse systems’ unique characteristics and needs.
The Future of Predictive Maintenance with ML
Machine learning technology is continuously evolving, and maintenance practices might look completely different a few years from now. Here, we list the latest advancements in ML for predictive maintenance that industry experts expect to be the most influential in this process.
Edge Computing
Used for real-time decision-making, edge computing already plays a pivotal role in the evolution of predictive maintenance. By processing data closer to the source, on the network’s edge, ML algorithms can make real-time decisions without the latency associated with cloud-based processing. This shift towards edge computing ensures immediate responses to potential issues, minimizing downtime and maximizing operational efficiency.
Digital Twins
The concept of digital twins, currently in its early stages, is set for rapid growth. Companies will increasingly adopt digital replicas of various physical assets, such as manufacturing equipment, power plants, buildings, and vehicles. This approach will allow for more accurate simulations and predictive modeling, enabling businesses to better understand and optimize these assets’ performance. This technology is anticipated to improve maintenance strategies and provide a comprehensive understanding of asset behavior over its lifespan.
Explainable AI
As the reliance on AI and ML algorithms grows, so does the need for transparency in decision-making. Explainable AI is dedicated to making machine learning models more interpretable. This is vital in predictive maintenance because it ensures that the recommendations and insights provided by ML algorithms are clear and easy to check. When dealing with equipment and systems, knowing why a certain prediction is made becomes essential for trust and effective collaboration between humans and AI, facilitating more informed decisions.
Autonomous Maintenance Robots
While this is a long and costly transition, the future of predictive maintenance is likely to see the integration of autonomous maintenance robots into the industrial landscape. These robots, equipped with ML algorithms and advanced sensors, will conduct routine inspections, identify potential issues, and perform minor repairs. This shift towards autonomous maintenance aims to reduce human exposure to hazardous environments and partially solve the human talent shortage.
The Strategic Advantage of ML in Predictive Maintenance
Modern and efficient Industry 4.0 maintenance strategies are inevitably interconnected with machine learning, at least for the foreseeable future. With ML algorithms, the approach to maintenance will be able to evolve from a reactive model to a proactive and predictive one. Businesses incorporating ML can plan maintenance activities strategically, reducing downtime, minimizing costs, and contributing to a more sustainable and efficient operational ecosystem.
If you decide to explore this opportunity, Beetroot, with our skilled teams specializing in ML, is ready to become your reliable tech partner. With our collaborative approach, we can empower you to harness the full potential of enhancing maintenance strategies with ML. As Industry 4.0 continues to unfold, we are here for you to explore the possibilities of machine learning together and start a journey towards a more sustainable and technologically advanced future.
Subscribe to blog updates
Get the best new articles in your inbox. Get the lastest content first.
Recent articles from our magazine
Contact Us
Find out how we can help extend your tech team for sustainable growth.